Notes From the Field: Five Common Framing Errors and How to Avoid Them
I spend a lot of time in the field consulting with builders and observing jobsites, and I see plenty of framing contractors making the same mistakes. Fortunately, they're easy mistakes to avoid. The key is understanding that each engineered wood member has a strength direction and, like solid wood, expands when it absorbs moisture. What follows are the five most common errors I see. For each, I reference a downloadable resource that details the correct practice. These resources and many more are available through the Resource Library at apawood.org.
1/ Sheathing installed incorrectly
The span ratings on a panel's grade stamp assume that it's installed in the correct orientation over three or more supports.
Orientation. The plies or layers in a sheet of plywood or OSB are oriented in cross laminations, typically with the grain on the face and back running in the long direction of the panel. Because wood’s strength runs with the grain, the panel is stronger in one direction—usually along the long axis. That means for optimum performance, it must be installed perpendicular to framing members. (Some panels are stronger along the short axis, but will have arrows indicating that fact.) Improper orientation reduces the panel's design capacity.
Support. The panel's span rating assumes that it's supported by at least three framing members. Panels with just two supports are more likely to sag and buckle under load.
2/ Sheathing cut too narrow
Sheathing is sometimes ripped to less than 24 inches and not properly supported. A narrow-width panel will deflect more than one 24 inches or greater in width. These panels are often installed on roof ridges, where workers are likely to walk during construction. The addition of blocking or edge-support clips will provide narrow-width panels with the support needed to resist the required loads.
3/ Notches and holes in the wrong places on framing members
While some holes and notches are allowed, holes and notches in the wrong place on a glulam or LVL member can significantly reduce its load-carrying capacity. There are clear guidelines on where notches can be made and how big they can be to maintain structural integrity.
Oversized or haphazardly drilled holes will weaken any framing member. So be sure to check the guidelines on where holes can be drilled in I-joist webs, as well as how big they can be. The flange, of course, must never be cut.
4/ Upside-down glulams
When glulam beams are manufactured as unbalanced beams, there are different bending stresses assigned to the compression and tension zones, and the beams must be installed accordingly. Getting this right is simple: When “Top” is stamped on the top lamination, that surface of the beam should be up.
5/ Panels not gapped in floor, roof, and wall sheathing
I see a lot of floor, roof and wall sheathing panels butted tight to one another. When they absorb moisture and swell, they can buckle. It's not always a structural issue, but it is an aesthetic issue and will make for unhappy customers.
To prevent this, panels need an 1/8-inch gap between them. Use metal H-clips where panels span joist or rafter bays. Where they meet over framing, use 10d box nails to make the gap. In underlayment installation, APA recommends spacing of 1/32 inch at underlayment butt joints.
Structural specifications for every piece of engineered framing include installation guidelines. Understanding these guidelines will help the framer avoid mistakes. The rewards are ones that every builder wants: fewer callbacks and more satisfied customers.
About the Author
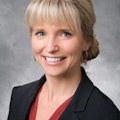
Karyn Beebe
Karyn Beebe, PE, LEED AP, is an Engineered Wood Specialist serving the Southwest. Her duties include consulting with designers on the efficient specification of engineered wood products in construction. A licensed professional engineer in the state of California, Beebe graduated from Purdue University with a degree in civil engineering. She is an active member of the Structural Engineers Association of California (SEAOC) and the U.S. Green Building Council (USGBC), and also serves as past president for the San Diego Area Chapter of the International Code Council (ICC). Before joining APA, Beebe worked as a structural engineer and structural plan reviewer for the San Diego building department.